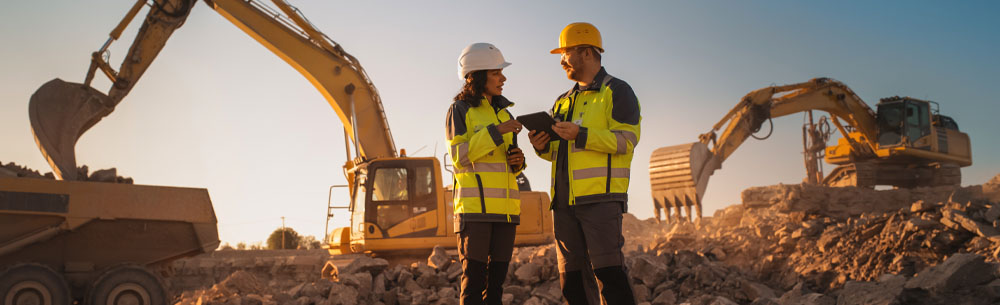
Content Warning: This guide contains statistics involving suicide and includes avenues to help employers and their employees address mental health concerns.
The health and safety of your workers should always be the top priority. But concern for workers’ safety shouldn’t be limited to project-specific hazards. Your company must also put in the effort to instill a strong safety culture and create an effective safety program to help workers be proactive when it comes to safety.
Your company’s safety impacts its public perception, amount and severity of workplace incidents, insurance premiums, ability to win bids on larger projects, potential to attract talented candidates for jobs and much more.
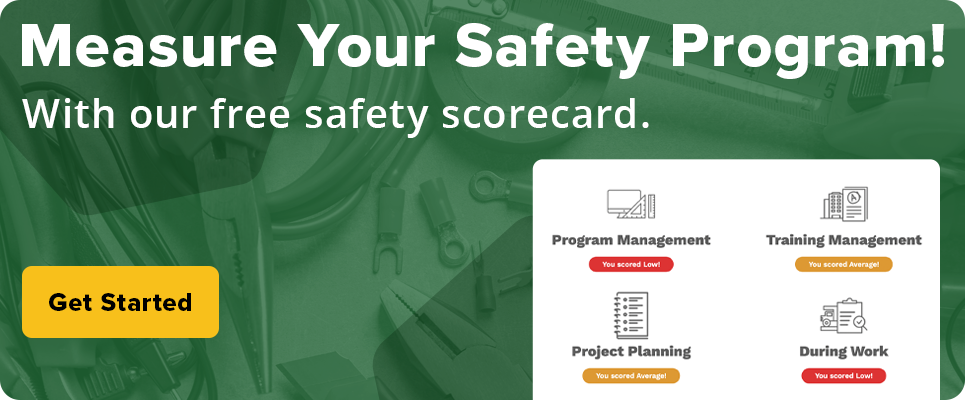
In addition, the Occupational Health and Safety Association (OSHA) has its own set of strictly enforced regulations. Each infraction carries a significant fine or penalty. OSHA’s 2024 memo outlines fines related to other-than-serious violations, such as posting requirements or failure to abate, as $16,131 per violation. Additionally, willful or repeated violations could carry a total of up to $161,323 per violation.
To keep workers safe and meet these regulations, construction companies need to have their own safety programs and procedures. Developing these processes and assessing their performance can be overwhelming — especially if a company doesn’t know where to start. That’s why we’ve compiled everything you need to know about construction safety into a free guide.
Article Highlights:
- Learn the importance of construction safety, identifying safety concerns and how to mitigate them.
- Discusses the safety manager’s responsibilities and how it affects the entire organization.
- Receive step-by-step guidance on how to build your own successful, engaging safety program.
- Learn how to create a strong safety culture and how to measure safety success.
- Explains how construction safety software simplifies safety.
What is Construction Safety?
Construction safety involves the well-being of construction employees when, and while, performing work on a jobsite. Safety is always a topic of discussion due to the inherent risks involved in the construction industry. Construction safety is measured by multiple factors like number of incidents in a year and annual inspection ratings.
In order to reduce incidents and mitigate risks, finding ways to establish and maintain a safety, like by hiring a dedicated safety professional, such as a safety manager, is crucial to maintaining safety.
What is a Safety Manager?
A safety manager, also commonly referred to as a safety director, is responsible for ensuring safety guidelines and procedures are clearly established and followed by the company and its employees. Safety managers provide workers and their supervisors with potentially life-saving information, ensure OSHA compliance by reviewing and submitting relevant documentation, schedule Toolbox Talks and make sure training and certifications are up to date.
Smaller companies may not have a dedicated safety manager. However, they should designate an employee, or committee of employees, to oversee their safety program.
Why is Construction Safety Important?
Aside from the obvious answer — the well-being of employees and the general public — there are a few reasons why construction safety is so crucial.
Increases Productivity
A safe jobsite means that workers can focus more on the task at hand and less on attempting to mitigate hazards on an individual basis. Also, employees who feel safe are generally more positive, which leads to them being more productive. Workers in unsafe environments generally feel uneasy and distracted from the task at hand.
Reduces Incidents
Following proper construction safety guidelines reduces the likelihood of workplace injuries and other reportable incidents. Informed employees generally take less risks because they can more easily identify hazards, and they are aware of safe, efficient methods when completing their tasks.
Improves Employee Retention
Amidst the construction industry’s current labor shortage, retaining qualified employees has never been more crucial. Safety is one of the most important factors in retention. Employees who know their company is taking steps to keep them safe and who feel their concerns are addressed are less likely to search for a new job.
Attracts New Employees
With more than 400,000 job openings in the construction industry [2], potential candidates have more options than ever. They want to know their safety is important to prospective employers. Construction companies who have many incidents will have a more difficult time attracting new, skilled workers because candidates frequently look for employers with less reported incidents during their job search.
What are Some Common Construction Safety Concerns?
Safety concerns can be divided into three sections: field safety, mental health and proper review of safety procedures to maintain compliance with OSHA standards.
Field Safety
Field safety is the hands-on approach workers take to protect themselves on the jobsite. Wearing the proper personal protective equipment (PPE) is a common example of field safety. Additionally, field employees who work at elevated heights use harnesses to mitigate the risks associated with falling.
Common field safety concerns include:
- Falls
- Hazardous materials
- Being struck by an object or equipment
- Electrocution
Non-fatal injuries suffered in the field cost the construction industry nearly $11.4 billion on average each year, according to Liberty Mutual Insurance’s 2023 Workplace Safety Index.
Mental Health
Mental health in the construction industry is oftentimes overlooked by company leaders, supervisors and workers alike. However, the construction industry has one of the highest rates of suicide at 53.3 per 100,000 U.S. workers — which is four times higher than the national average and five times higher than all other construction fatalities combined [3]. This statistic is driven by a variety of factors, some of which include working conditions, chronic pain, drug and opioid abuse and a reluctance to seek help from others.
Addressing mental health concerns involves vulnerability from the employee who is affected as well as others within the company. Each employee must feel they are in a safe environment with people who understand them and are willing to listen to their concerns. The Construction Industry Alliance for Suicide Prevention believes each construction company should have a mental health program separate from a traditional safety program to put an emphasis on mental health.
Using resources — like the Needs Analysis & Implementation Tool provided by the Construction Industry Alliance for Suicide Prevention — to develop your own mental health program could save lives and improve employee morale.
Proper Review and Distribution of Safety Procedures
OSHA created guidelines that cover the specific information that needs to be included in a construction company’s safety program. However, the means in which this information is delivered to employees is left up to each construction company. There are a few common, effective ways to distribute this crucial safety information:
- JHA and corrective action documentation
- Toolbox Talks
- Equipment inspections
Once completed, this information must be reviewed by a supervisor, safety manager or, if applicable, the safety committee.
Safety Programs — What are They, and Why are They Important?
Safety programs establish your company’s stance on safety, and they provide actionable steps to help keep your workers safe and ensure your company remains compliant with local and federal guidelines. A successful safety program should be an extension of the safety manager or safety committee. It should be engaging, educational and easy to understand.
There are several costs related to safety programs: paying someone to oversee safety, investing in a construction safety software or if your company doesn’t use software, you consider the costs of printing and distributing materials related to the safety program.
With all these costs, creating a construction safety program can seem like a financial burden. However, according to OSHA, for every dollar a company invests into its safety program, it receives an average of $4 to $6 in returns by avoiding workplace illnesses, injuries and fatalities.
How Do You Implement a Successful Safety Program?
While creating a successful safety program can seem like a daunting task, it’s crucial for your company’s long-term success. Establishing a safety program can help reduce workplace incidents, workers’ compensation claims, avoid hefty OSHA fines and penalties and, ultimately, leads to a more productive workforce.
Identify Hazards
Hazards should be outlined in a jobsite hazard assessment, or JHA, so field employees know where hazards are located and the proper procedures to mitigate or avoid the associated risks.
Provide Safety Training
There are several training courses provided by OSHA to help educate field personnel on best practices. Additionally, Toolbox Talks deliver crucial safety information to your employees in a hands-on environment. Companies that conduct daily Toolbox Talks reduce their total recordable incident rate (TRIR) by 78% [1].
Keep an Open Safety Dialogue with Employees
Employees should know their safety concerns are not only heard but addressed by their supervisor, safety manager or the safety committee. Your company should clearly define its safety contacts for employees and the process of reporting safety concerns.
Additionally, you should follow up with employees to inform them of solutions or ways to mitigate their concerns. Providing safety transparency will make employees feel more engaged with safety, increasing productivity, reducing incidents, improving retention and attracting new skilled employees.
Looking for a more basic breakdown? Check out these steps:
- Establish employee safety and health as a fundamental company value.
- Create a collaborative safety committee.
- Clearly define a system for questions, concerns and incident reporting.
- Provide engaging training and certification opportunities for your employees.
- Regularly inspect the workplace or jobsite for hazards.
- Gather hazard control ideas from employees.
- Review the hazard control ideas and establish standard operating procedures to mitigate or avoid hazards.
- Create company-wide safety goals.
- Delegate safety tasks, implement the safety program and ask for initial feedback from your employees.
- Regularly assess safety performance and make improvements to the safety program.
What is the Importance of Building a Strong Safety Culture?
OSHA is allowed to perform unannounced inspections, which can result in substantial fines for companies who are not adhering to their standards. According to OSHA, more than half of its 31,820 inspections in 2022 were unplanned.
One common OSHA standard involves form 300-A, which is an annual summary of work-related injuries and illnesses. This information is visible to employees at the end of the year and can be crucial to retention. It can also be a helpful indicator as you try to improve your company’s safety.
When it comes to reducing work-related injuries and illnesses, providing the education and training is the easy part — the challenge is getting the buy-in from every member of the company that results in improvement. That’s where creating a strong safety culture comes in.
Workers can be as informed and educated as OSHA guidelines require, but that alone can have a limited impact on your company’s safety. That’s because without a strong safety culture, safety can become an afterthought to project timelines.
According to EHS Today, 67% of employees believe that productivity standards are higher than safety standards. This puts employees in a challenging position. Do they cut corners from a safety standpoint to meet the project timeline, or do they follow safety guidelines and miss a key project deadline? Most employees go with the former, stating they feel it’s the best way to keep their job or advance within the company. This mindset can lead to an increase in workplace safety incidents.
To reduce this issue, your company should take a safety-first approach from the top down. If your company is trying to establish a strong safety culture, it should clearly state that safety is the top priority and provide actionable steps within the safety plan to support this idea. For example, employees should be told where to report safety concerns and should understand how those concerns are addressed by the safety committee or safety manager.
Additionally, it’s important to mold new employees to fit into your company’s safety culture. According to ABC’s 2023 Safety Performance Report, new hire orientation that features safety procedures reduces TRIR by 48%-52% in comparison to companies who do not offer it. (Check out 10 Topics to Cover When Training New Construction Workers for more information!)
How Can You Make Safety Engaging?
Delivering safety training that resonates with your employees is crucial to improving safety. Here are some tips to help you keep your employees engaged:
- Assess Your Current Plan
Do you rely mostly on safety presentations and handouts? Do your workers seem generally disinterested? Evaluate your safety program and determine areas for improvement.
- Implement a Hands-On Approach
Most workers benefit from a more hands-on approach to safety training with controlled, simulated situations that allow them to learn from potential mistakes and apply safety standards themselves.
- Rotate Safety Speakers
Safety lectures are sometimes unavoidable. When this is the case, consider inviting guest speakers or having rotating speakers from the safety committee talk to the group. Additionally, ask the group questions and maintain a more conversational approach.
- Send Pre- and Post-Meeting Handouts
Providing employees with engaging information that includes visuals and statistics before a meeting can help them familiarize themselves with crucial information, engage during safety meetings more and ultimately, help them establish better safety habits.
- Ask Employees for Feedback
You should always strive to improve your safety program. Suggestions from employees can help you keep your approach to safety fresh and engaging.
For a more comprehensive overview of creating an engaging safety plan, click here.
How Do You Measure Safety Success?
Once the safety program is implemented, it’s important to regularly assess its performance. Using past and present safety data, you can determine several key performance indicators to discover areas of improvement.
Experience Modification Rating (EMR)
The EMR is used as an important calculation when determining premiums for a contractor’s insurance and workers’ compensation program. EMR takes into consideration less severe injuries that are not reported to OSHA, such as a first aid injury that required a workers’ compensation claim. The higher the EMR, the more a contractor has paid in workers’ compensation.
Tracking EMR is a great way to capture a comprehensive picture of safety for a contractor, address safety concerns and reduce workers’ compensation claims. Your insurance agency is legally obligated to provide your EMR, and your updated rate is available at the beginning of the fiscal year.
EMR starts at a baseline of 1.0. A 0.9 EMR would mean you received a 10% reduction on your premium for your company having lower-than-average workers’ compensation claims. A 1.1 EMR would mean your premiums cost 10% more than the average because your company had higher-than-average workers’ compensation claims.
Days Away, Restricted or Transferred (DART)
DART is divided into:
Days Away – Days an employee can’t work at all.
Restricted – Days employees can only work in a limited capacity.
Transferred – Days an employee spends working in another department due to an injury.
DART rate determines the frequency in which DART incidents occur at your company.
DART Rate = Total Number of DART Incidents x 200,000
Total Number of Hours Worked by Employees
*This equation produces a rate per 100 full-time employees.
Lost Time Incident Rate (LTIR)
LTIR is similar to days away; however, LTIR focuses on more severe injuries. LTIR can be used as a good indicator to see how workplace injuries affect a contractor’s productivity.
LTIR = Lost Time Injuries x 200,000
Total Number of Hours Worked by Employees
*This equation produces a rate per 100 full-time employees.
Total Recordable Incident Rate (TRIR)
TRIR measures recordable workplace incidents, which can help determine the success of a safety plan across multiple past projects. OSHA also uses TRIR to measure the success of a contractor’s safety practices. Additionally, it can be a helpful metric to predict future outcomes. A high TRIR will likely mean more OSHA inspections and fines, whereas a low TRIR indicates that workers have a heightened safety awareness and follow guidelines.
TRIR = Number of OSHA Recordable Injuries x 200,000
Total Number of Hours Worked by Employees
*This equation produces a rate per 100 full-time employees.
Using EMR, DART, LTIR and TRIR you can analyze your past, current and potential future safety metrics. You can also pair these calculations with your incident reports, JHAs and employee training and certification data to determine areas of improvement for your safety program and help identify and reduce excess costs.
How Can Construction Safety Software Help Improve Safety?
Construction safety software is a digital solution that stores, distributes and tracks key safety information to help facilitate a safer, more efficient workforce. It streamlines every office process related to safety.
Key Features of Construction Safety Software
Trying to find specific safety information, track results and submit reports to the proper regulatory agents can be a time-consuming challenge. With construction safety software you and your team can:
- Easily find and store JHAs, incident reports and other important safety data in one secure location.
- Distribute pre-built safety resources or customize them based on each job.
- Track the completion of training and certifications.
- Receive notifications about specific safety tasks, such as mandatory safety meetings and reminders to complete job-specific safety trainings.
- Pre-populate safety data for incident reports.
- Educate your team with the click of a button.
- Automatically file required OSHA forms, such as the OSHA 300A.
- Create, distribute and track the completion of Toolbox Talks.
- Access a library of millions of Safety Data Sheets.
Benefits of Construction Safety Software
In addition to the features listed above, construction safety software offers a variety of unique benefits, such as:
- Establishing and maintaining safety consistency across your company.
- Reducing time spent on administrative tasks related to safety.
- Increasing safety data visibility to assess safety performance more easily.
- Putting more engaging educational safety information in your employees’ hands.
For a more in-depth breakdown, click here.
What Should You Look for When Choosing Construction Safety Software?
Selecting the right construction safety software for your operations can seem intimidating. While the right construction safety software can save you and your team time and money, the wrong software could provide inaccurate data or make tracking information more difficult. This could lead to costly mistakes, such as OSHA fines.
To find the right construction safety software for your operations, follow these basic steps:
- Speak with members of your team and create a list of features that are must-haves.
- Start researching options and compile a short list of software for further evaluation.
- See if the software has any free webinars or demo videos available on their websites or YouTube channels.
- Schedule multiple demos with the software companies you feel could best fit your needs.
- Compile questions for the demo, namely feature-specific and customer service questions.
- See if the construction safety software company has references you can speak to about the quality of the software and the type of customer support they receive.
- Select the best construction safety software based on the demos and answers to your questions.
Finding a safety software that is specific to the construction industry can be a challenge. Some software, like SafetyHQ®, offer easy-to-use interfaces with real-time reporting for job hazards, safety certification tracking, a library that includes millions of product documents and pre-built and customizable Toolbox Talks.
What are the First Steps to Improve Your Company’s Safety?
Safety is the most important aspect when working in the construction industry. Understanding this is crucial, not just to avoid incidents but to attract skilled workers, retain employees, improve productivity and cultivate long-term success. Review your current safety program and note areas for improvement. Then determine if your company has the time and support to implement these changes manually or if a construction safety software would be a better solution for your situation.
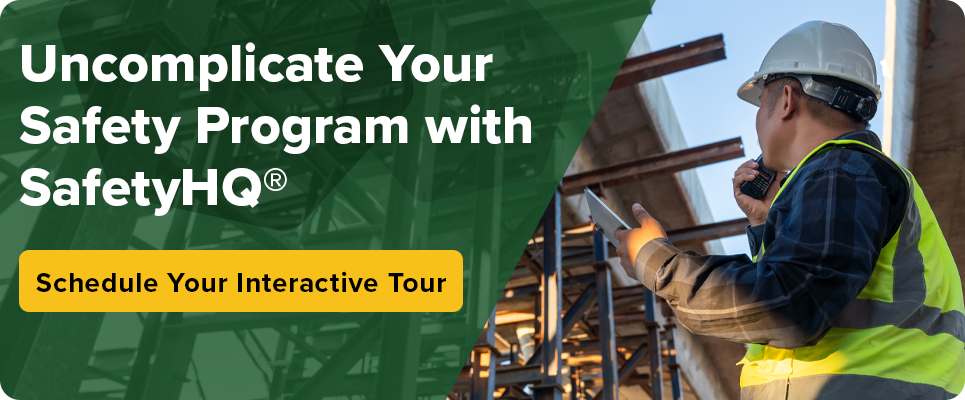
[1] – ABC’s 2023 Safety Performance Report
[2] – AGC’s Mental Health & Suicide Prevention
[3] – Bureau of Labor Statistics Workforce Statistics from January 2024
Share Article
Keep on current news in the construction industry. Subscribe to free eNews!