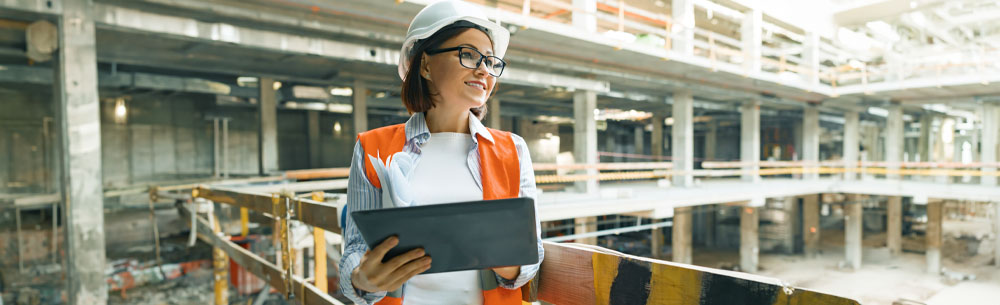
I am willing to bet that you own or work for an established construction company that already has a basic safety program in place. If I am wrong, then you should definitely email me (sue@mysafetyhq.com), and I will pay out that bet to a charity of your choice. Then, you should switch over to my other article: 5 Easy Tasks to Start Your Construction Safety Program, and come back here when I’m not going to lose that bet again.
The reason you are still reading must be because you know your safety program can and should be better; you just don’t know how to achieve that. Don’t worry, I’m here to help you take it to the next level.
Here are 5 tasks that will improve your existing safety program:
1. Conduct Job Site Hazard Assessments
A Job Site Hazard Assessment (or JHA) is essentially a safety plan conducted by the foreman on site before work begins. It asks them to record the tasks they will work on that day and then generate a list of potential hazards that may arise from those tasks. Once they know what the hazards are, the final step is to design and implement a plan to eliminate, contain, or reduce each hazard.
Having your foreman complete a JHA every morning puts safety front of mind on site and gives them practical ways to keep themselves safe. Additionally, it reduces your company’s liability in the event an incident were to occur.
This is especially true if a worker is negligent in using the safety measures from the JHA because you will have written proof of what they were advised to do. This ten-minute daily exercise can literally save lives and lawsuits.
2. Host Safety Meetings with the Whole Team
Ideally, your foreman should already be conducting a weekly Toolbox Talk with their crew on site in small groups. The next logical step is to run a similar meeting on a larger scale, which delves deeper into a safety topic or issue and includes your entire workforce on a monthly or quarterly basis.
Select a topic for the theme of the meeting that is relevant to your trade, starting with the more common hazards. For example, a roofing company may start with ladder safety and personal fall arrest systems, whereas an electrical company would begin with something such as a lockout/tag-out.
You may also consider tackling topics that are trending in your documented infraction notices. If your team seems to be forgetting to wear safety glasses, you could focus on hazards related to eye and face protection.
If you have a dedicated safety person, they should be the ones running the meeting, and if not, they should be a person as high up as possible. In fact, all members of the management team should participate when possible and, at a minimum, be in attendance. The more your workforce sees your commitment to safety, the stronger your safety culture becomes.
To keep things fresh and interesting, consider inviting a guest speaker. This could be a safety expert from the community, someone who has experienced a workplace incident, or an expert such as an ER doctor to talk about head trauma. I once attended a meeting with a police officer as a guest speaker about defensive driving techniques. The workers were hesitant at first but were asking him tons of really good questions by the end.
These safety meetings are also an excellent opportunity to publicly praise or even hand out prizes to your safety leaders for that month.
3. Provide and Track Training
The best place to start your training program is by figuring out which training you should be providing and tracking. This will be different depending on your trade. Take a look at all the hazards your crews are recording on their JHA’s (outlined above in point 1) and use that to generate an exhaustive list of potential hazards.
Then go through the list and highlight the ones that are:
- Most likely to occur based on how often the exposure occurs (i.e. painters exposure to chemicals)
- Are most likely to result in serious injury or death if they do occur (i.e. silicosis for masons)
- Both (i.e fall from heights for roofers)
The highlighted list of hazards is where you should be providing training, with your focus being on any in the third category. The rest of your hazards can be covered during Toolbox Talks and Safety Meetings for now.
If you are a Canadian contractor, the IHSA provides a Training Requirements Chart as to what you are legally required to do, but the activity outlined above still doesn’t hurt.
If you are American, OSHA provides a basic training program called OSHA10, which is a good idea to have your workers complete but does not cover the hazards specific to your trade. The states of Nevada, Missouri, New York, and Connecticut have actually made OSHA10 mandatory for all construction workers.
Now that you know what you need to cover, you can schedule your training. You do not need to teach this training yourself. We highly recommend hiring a safety professional to provide it for you. Most will join you at your office or shop and train your staff all together.
Once complete, the last step is to record who took the training, when, and the date it expires. Tracking this information means you can stay on top of training before it expires and can provide it to authorities in the event of an incident or a site inspection.
4. Inspect all equipment
Conducting both formal and informal inspections of your equipment will reduce the likelihood of an incident and also save your company time and money. A malfunctioning piece of equipment can very easily slow down or halt production on your job site and cause injury to your workers. An issue that is caught and resolved during an inspection can save you the costs of replacement, lost time, and maybe even the life of your employee.
An informal inspection is completed by the person who is about to use the equipment. It is in their best interest that the inspection is completed as it will most likely be them that is affected if an incident were to occur. This inspection is done to ensure all the parts of the equipment are accounted for and functioning properly. It does not need to be documented unless an issue is found.
A formal inspection is conducted in addition to the informal one, usually by a supervisor or safety personnel. The date, serial number, and results of the inspection are recorded, regardless of whether the item passes or fails. Some companies mark their equipment with a name (ie Cordless Drill 15) to make tracking easier.
The management team can then make sure every piece of equipment is inspected on a regular basis. Striving to have each item inspected once a month (at a minimum quarterly) is a pretty reasonable goal or expectation.
The types of equipment that should be included in these inspections are:
- Safety equipment (i.e. personal fall protection systems, fire extinguishers, first aid kits)
- Power, Pneumatic, and Hand Tools (i.e. drills, saws, hammers)
- Non mechanical equipment (i.e. ladders, scaffolding, wheelbarrows)
- Mechanical equipment (i.e. compressors, generators, rock vacs)
- Machines (i.e. forklifts, cranes, aerial lifts, skid steers)
- Vehicles (including trailers)
5. Conduct Job Site Inspections
Most likely, you already have a supervisor who manages multiple job sites. They are probably already visiting the site to check up on the crews and track production. There is no reason why they can’t do a Site Safety Inspection while they are there.
They should be looking for worker compliance with safety protocols, such as proper personal protective equipment, safe use of equipment, and proper material handling. You can generate a list of areas that they should focus on by revisiting the list you created when setting up your training program, outlined above in point 3.
This is a great time for the supervisor to review the JHA that was completed by the crew at the start of the day and make workers aware of any unexpected or unusual hazards that weren’t noted. It is also an excellent opportunity for on-site teaching and to make suggestions on safer ways to work.
These inspections should be recorded and handed to the management team for review, even when there are not any issues noted. The data collected in these reports is going to be invaluable when management decides they want to analyze and track anything safety related.
This All Feels Like a Lot of Work
I know, and I get it. In all likelihood, you are ‘in charge’ of safety, but that isn’t all you are in charge of. When I was working at a construction company, my primary responsibility was running the service department, and for some reason, safety was thrown in my lap, and I’m not even sure why; it’s possible ‘Service’ and ‘Safety’ just sounded good together.
I didn’t have a safety background or the time to manage such an important duty. The key to my survival was delegation. Everything listed above does not (and, in fact, should not) fall on you. The foreperson of each crew should be conducting the JHA’s and their supervisors should be doing the site inspections. Equipment inspections need to be everyone’s responsibility, but the formal ones can also be assigned to supervisors or even a back shop manager. You may need to set up the training program, but once established, pass on the tracking and scheduling of training to someone on your Admin team.
Safety meetings are likely the only task listed that you need to take full ownership of. Other than that, someone needs to collect and track the paperwork that is about to be generated. This is the area that I had the most difficulty with, and that is why I turned to technology to help.
How SafetyHQ Can Save You From Drowning in Paperwork
SafetyHQ Software is an App that completely eliminates paper from the safety process. Inspections that are conducted on-site are done on the foreperson’s phone or tablet and immediately stored and available to office personnel. It comes complete with the following modules to make setting up and managing your safety program easy:
- Forms / Inspections
- Equipment Tracking
- Lessons / Learning Guides
- Training Management
- Document Storage including all your manuals and safety data sheets
Best of all, SafetyHQ comes complete with a dedicated customer success manager who is personally available to help you set everything up and to train you on how to use it. Basically you get access to me as much as you need!
If you want to see SafetyHQ in action, click here to book a demo. Otherwise you’ll probably find these articles helpful:
What is a JHA? (Definition and Usage)
The 6 Best Construction Safety Apps – Ditch Paperwork Forever
How Much Does SafetyHQ Cost?
Share Article
Keep on current news in the construction industry. Subscribe to free eNews!