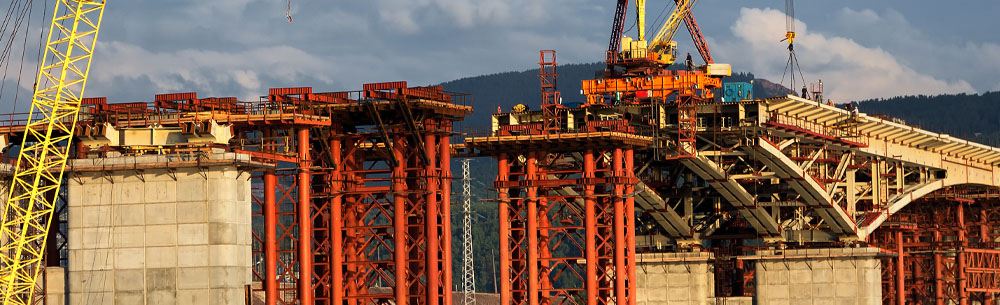
Nobody wants to put a safety manual together. It’s boring and tedious and, worst of all, incredibly confusing. A safety manual sometimes called a safety program, is the formal document that outlines your company’s safety mission and how you go about implementing it.
You’ve likely already been on the OSHA website and gone down a rabbit hole of link after link after link until, eventually, you forgot what your original question even was.
Then, just to make it that much more complicated, you find out there are 28 states that have OSHA Approved workplace safety and health programs, in addition to OSHA, and you must meet their requirements as well.
The problem is that there are so many variables that it’s hard to make all-encompassing safety regulations, for every contractor in every trade, in every state. But that sounds more like an excuse than anything and doesn’t help you at all.
Getting Started
Get started by getting something in writing because something is better than nothing. If OSHA knocked on your door tomorrow, at least you’d be able to hand over a document of some sort, which they will likely give you credit for.
We’ve summarized for you below what is most commonly included in a safety manual so you aren’t left staring at a blank page at the end of this. We’ve even provided you with a bunch of links to samples provided by OSHA themselves, so you can start by literally copying and pasting.
However, even OSHA puts a disclaimer on their samples that it’s not a one-size-fits-all situation. They want you to read through everything they give you and make changes based on your company specifically.
Key Elements of a Safety Manual:
1. Company Safety Policy
A safety policy is written by (or at least approved by) the owner, COO, or President of your company. It is usually about a page long and expresses their commitment to making worker safety a core company value.
It may also include the motivation or reasoning as to why the policy is in place, which can simply be: to comply with OSHA and state regulations and to prevent employee injury and illness.
It’s important that the policy is personally signed by the highest level of management so that everyone knows the policy is in place from the top down. Best practice says it should be updated and re-signed annually.
Some sample policies are provided by OSHA on page 48 of their Small Business Handbook.
The remainder of your safety manual outlines how the company is going to honor the commitments in the policy you just created.
2. Safety Responsibilities
A safety manual should very clearly define exactly what is expected of each employee. In order to account for employee turnover, this is best broken down into roles. Here are the most common roles and some sample responsibilities to get you started:
- The Employer
- cover the costs of PPE
- factor in time and resources for safety within each project
- provide access to safety documentation (SDS, injury data, inspection findings)
- Provide general and trade-specific safety training
- Comply with local safety regulations as well as company policy
- Fully investigate incidents
- Supervisors / Management
- Comply with local safety regulations as well as company policy
- Maintain and wear proper PPE
- Report safety issues to upper management
- Ensure crew compliance with rules
- Report all accidents/incidents/near misses
- Work in a manner that does not endanger others
- Take every reasonable precaution to prevent personal injury
- Conduct toolbox talks, site inspections, and JHA’s
- Employees
- Comply with local safety regulations as well as company policy
- Maintain and wear proper PPE
- Report safety issues to supervisor
- Report all accidents/incidents/near misses
- Attend safety meetings
- Actively participate in ongoing safety training
- Work in a manner that does not endanger others
- Take every reasonable precaution to prevent personal injury
Make sure you add in any additional responsibilities for your company and feel free to create more roles. As you can see above, there should be an overlap of some of the duties, providing a sense that safety is everyone’s responsibility.
3. Hazard Identification and Controls
This is where your trade really comes into play. A plumber is going to experience very different hazards than, say, an excavator; and the excavator, different than a framer. Luckily, this section does not need to cover every single hazard your team may run into but the most common ones they are exposed to.
Start by generating a list of hazards specific to your trade. If you need some help getting started, take a look at OSHA Standard 1926 for a list of regulations specific to construction.
The list is not easy to navigate, but if you scan through each lettered subpart (i.e., Subpart D), you’ll get an idea of the main categories. If the category applies to your trade, review the regulations within it for ideas.
For each hazard, you then need to include a control method. Try and use the most effective control (elimination) whenever possible and the least effective (PPE) as a last resort.
(image source: Niosh)
Finally, there are four hazard types that OSHA states must have written plans in place if your trade is exposed to them, even if it’s a rare occurrence. I have listed them for you below with a direct link to the regulation so you can determine if it is applicable to your company.
If the hazard is relevant to your company, you must include it in your safety plan. Some regulations specify what must be included in the written plan, so it is important to read these four regulations.
Thankfully, OSHA offers sample plans for each of these hazards, which I have pulled from the rabbit hole and linked for you as well.
- Bloodborne Pathogen Exposure Program
- Permit Required Confined Spaces
- Hazard Communication Program
- Respiratory Protection Program
4. Safety Procedures / Best Practices
This section is used to outline the proper, safe ways to complete common tasks.
For example, if you are a masonry contractor, moving bricks is not likely the most hazardous task you complete, so it wouldn’t be covered in the section above; however, if not done properly, over time, it could lead to back issues.
In this case, a written procedure on how to transport and carry bricks safely will protect your employees from a repetitive strain injury.
Other processes you may wish to include would be the use of hazardous machines or tools.
You don’t have to reinvent the wheel. Once you have identified the procedures you’d like to outline, your local trade association very likely has a copy of the proper steps. Worst case, Google is your friend here.
5. Training
Your safety manual is useless unless it is put into action.
This section should outline how you are going to train all new and existing employees on your new safety program, covering each of the sections.
To do this effectively, most employers opt for a new employee onboarding program to cover all the knowledge and skills their employees require in order to work safely. Some even pair new employees with a mentor to guide them in the right direction during the first few weeks.
You should also include a list of formal training required based on which role they have been hired into. For example, you may require all workers to take a fall protection course but only your foremen to take first aid training.
Finally, you should describe how you are going to track who has taken what training and when it expires. This will ensure everyone’s certifications are completed and kept up to date (not expired).
6. Resources
The final section of your safety manual acts more like an appendix and should include any parts of the program that were not already covered. Some may include:
- Forms or inspections you use on-site
- Safety Data Sheets
- New Employee Orientation Package
- Manufacturer Safety Policies
If you have more than ten employees in your company, OSHA stipulates you must include An Emergency Action Plan (OSHA 29 CFR 1926.35/150) and a Fire Prevention Plan (OSHA 29 CFR 1926.24)
Basically, any document that is a part of your program gets added to the end of the manual, so there is one central place for all safety-related information.
What Now?
Now that you have a first draft of a formal written safety manual, I’d get a professional to review it. Here’s the great news, this doesn’t have to cost you a dime. OSHA offers a no-cost, confidential Onsite Consultation Program. Here are the benefits:
- The consultants are safety professionals from local state agencies or universities, NOT OSHA enforcement officers
- They are local to you, so can reference any state regulations
- The consultant will NOT report any violations to OSHA
- The consultant will review your safety manual and provide you with feedback specific to your company
- They will visit you onsite to help you identify common hazards and provide options to control them
- After the visit, they will send you a written report with all their findings and recommendations
The only obligation you have to the consultation program is a commitment to correct serious health and safety hazards in a timely manner, which is a responsibility of yours as an employer anyhow. There really is no downside.
Like any free program, there are going to be limits to the amount of time the consultant can spend with each of their clients. By having already written out your first draft of your safety manual, you will really make the most of their time with you and get the answers you need.
Extra Helpful Tips
Once you are happy with your written safety manual, you are going to need to make it available to your entire workforce. Lots of contractors print a copy and leave it in their break room, but that doesn’t help the workers who are onsite.
A Safety Management System like SafetyHQ can help you solve this problem and many others as you work to improve the safety culture at your company. Our Learning Center is a great place to google your questions, as I’m sure they will arise during the first draft.
Good luck, and remember, something is better than nothing, so just get started!
Share Article
Keep on current news in the construction industry. Subscribe to free eNews!